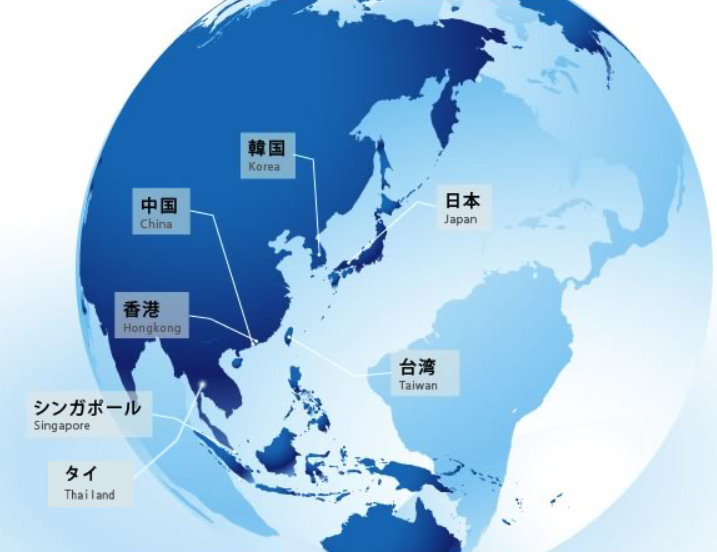
海外工場の購買事情に関して 220708
暫くぶりの更新になりますが、購買に関するトピックは直近特に力を入れて書きたかった記事になります。生技の業務を進めていくうえで加工品や購入部品は生産性改善のために欠かせないのですが、海外工場ではこのような部品の調達性の課題が多々あります。簡単に言うと、QCD全般の質が低く、低品質、高価、遅いの3重苦で、人件費が安いはずのタイでCostまで悪化してしまうのか理解に苦しみます。
自社購買の機能がイマイチだからこそたくさんの海外商社がご活躍されている訳で、国内事業所の購買課のパワーを改めて思い知らされました。
今回は、海外購買の実情について生技視点で記載していきたいと思います。
何故低品質になるのか
日本と同じ図面で同じ消耗部品を発注したとしても、海外で調達した部品は国内で調達した部品と比べて寿命が短いケースが多々あります。うちの工場では、マレーシアや中国の加工メーカへ依頼しているケースが多いのですが、部品の寿命が短くなるということは材料の硬度(HRC)等が図面の記載どおりになっていないように思います。おそらくメーカ側で加工しやすいように硬度を落としており、購買側も部品に求められる機能や耐久性を把握していないために加工業者との仕様の取り交わしができていないように思います。
購買課の担当者ですが、製造現場を理解しているスタッフがほとんどおらず事務的にワークフローを流しているだけのようですので、品質に関する調整をメーカと実施できない、そういった機能を購買課が持ち合わせていないです。
購買担当が要求仕様を把握していないため、加工業者の選定も適当になりがちで、完成品の品質を満足しているかどうかは博打になります。
何故部品価格が日本よりも高くなるのか
タイ国内で安定生産可能な加工業者があまり無いのではと推測しています。タイで加工できていれば人件費が安い分値段は下がるはずですので。うちの工場も
Misumi等を使用しますが、日本国内で加工されたパーツには関税が発生するため国内で
仕入れるよりも高価になります。
また、中国、マレーシア等の加工業者に依頼したケースにおいても国内の
仕入れ価格の3倍程度のコストとなっていることがあります。これについては購買課の価格交渉力が無いため相手の言い値でものを買ってしまっているように思います。ですが、小さな買いものであれば、部品価格についてはまだ目を潰ることができます。
何故部品調達に時間がかかかるのか
はい、これがこの記事で一番書きたかった内容になります。日本では購買依頼をかけますと遅くとも2、3営業日で発注がかかっておりますが、うちの工場では発注までの社内処理に2~4週間かかることがあります。
工場なのでスペアパーツの在庫切れ等で現場ですぐにモノが欲しいという時も購買の仕事の遅さによって生産が滞ってしまうことが多々あります。
これは生技担当からすると非常に腹立たしいことで、現場をサポートする立場の購買が現場の仕事を妨げているようにすら思えることがあります。
PO発行までのフローが生技担当からすると
ブラックボックス化していたため進捗がフォローできないという問題がありましたので、購買のフローの詳細を担当者に確認しました。
購買フローの詳細を下記に示します。
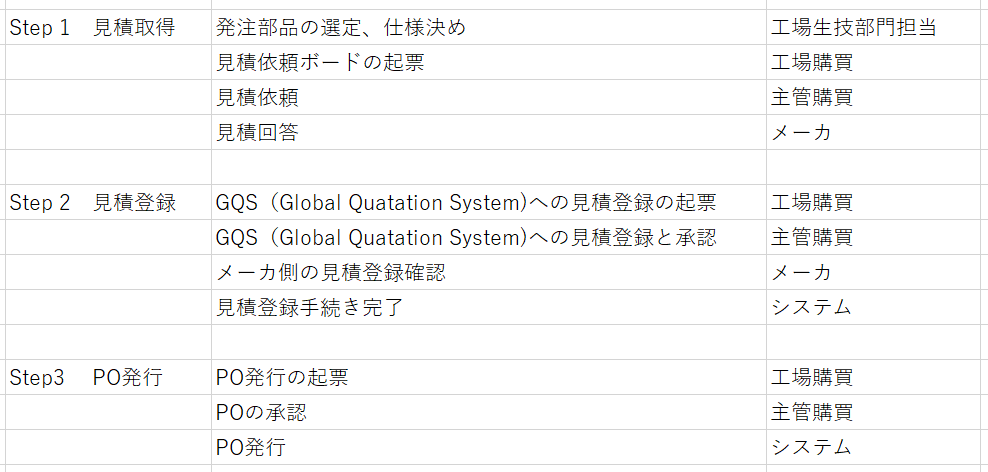
Step が3段階に分かれており、各ステップごとに部門承認が必要であるため普通に承認フローが流れたとしても見積依頼からPO発行までに2週間程度の時間を要することがあります。途中の何かしらの問題が発生して次のステップに進めない場合でも、担当者が途中で諦めて放置してしまっていたり、担当者に連絡を寄こしませんので進捗があるかどうか分からないことがあります。
ここで特異なことは、Step2の見積登録のフローは国内購買おいては存在せず、海外事業所のみのフローとなります。
メーカが提出した見積もりを、何故メーカが再度確認しなければいけないのでしょうか??普通に考えれば無駄なStepでしかありません。
その理由は少し考えれば見えてきます。
見積りを偽造されて会社の金を横流しされるリスクに備える必要がある
実際に海外購買担当者の不祥事は定期的に発生しており、それを防止するためにメーカの見積が正しいことをメーカ自身に確認頂く、かつメーカから承認された見積でしかPOが発行できないシステムが構築されています。
見積を改ざんしたとして担当者の懐に差額が得られるシステムを構築する必要がありますが、これは意外と簡単な方法でできてしまいます。
ここで敢えて書く必要があるか悩みましたが、読者の方には製造業のあらゆるリスクを知っておいて頂きたいですので、何らかの参考になればと思い私の聞いたことのある事例を記したいと思います。
以下、見積偽造による中抜きの模式図になります。
見積偽造まではしていませんが、これを両社合意の元で合法的に進めているのが商社になります。
海外で金を中抜きされて
横流しされてしまえば、我々日本人が金を取り返そうとしても現地の金融機関を把握していなければ追いきれない可能性がありますし、多額の損失が発生した場合は工場だけでなく
仕入先にも迷惑がかかることになり管理担当者にも責任を問われる事態になりかねません。海外購買においては、QCDの改善は二の次で会社の金を中抜きされるリスクを排除することを一番重視せざるを得ないため、多少仕事が遅くなるのは我慢するしかないのかもしれません。
購買問題の解決策について
以上、長くなりましたが海外購買の問題点とその原因についての考察になります。日本のような優れた購買機能を期待するのは難しいのですが、工場管理者としてはQCDの質向上のために購買にはしっかりと働いてもらう必要があります。
この一つの解決策の提案として、自社購買よりも優れたネットワークを持つ商社を利用して部品選定、見積までを行うという手があるように思います。海外工場においては自社購買に100%の信頼を持つことが難しいですし、そういう意味では外部の優れた商社に一部機能を代替してもらうという戦略も有効です。
意外にも自社購買でモノを買い付けるよりも安価な見積が得られることがありますし、スピード感は優れていることが多いです。
自社以外の購買ネットワークを何個か保有しておいて状況に応じて使い分けを行うことが上手な立ち回りのように思います。(自社購買課担当からは、商流が複雑になることや自分たちの領分を侵されるためよく思われないかもしれませんが…。)
今回のところは海外購買の課題感に軽く触れただけになりますので、今後さらに深堀できる機会があれば次回の記事にしてみたいと思います。